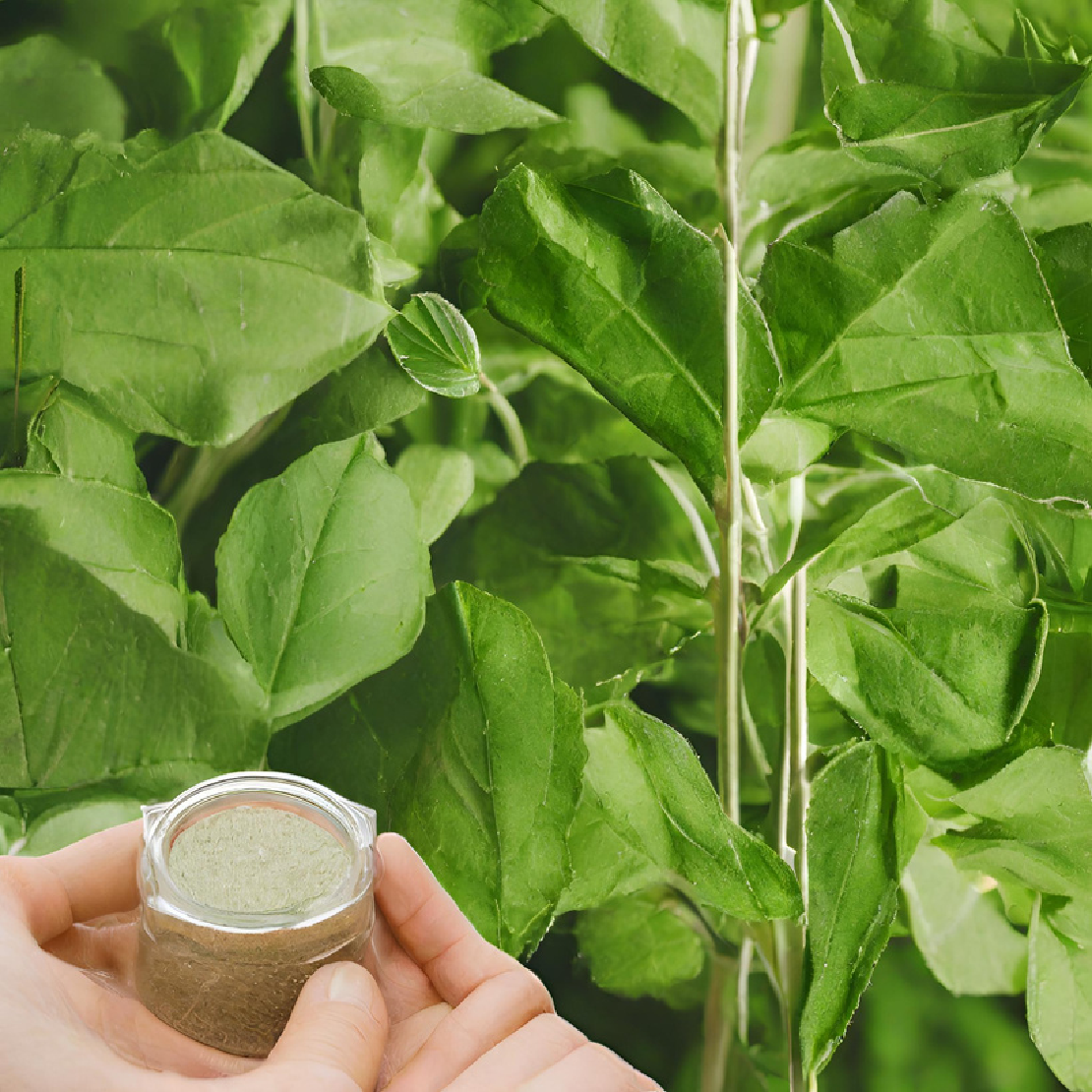
Difference between Green Procurement and Sustainable Procurement
With the rising concerns in environmental sustainability, procurement practices are very crucial in driving …
Circular manufacturing or circular economy is defined as a production and consumption model whereby manufacturers find methods to bring back materials into the economy instead of discarding them like in the normal linear manufacturing method.
In a world with rising environmental challenges caused by traditional linear manufacturing processes, a new paradigm is emerging—one that promises to completely transform the way we produce goods while reducing our impact on the planet. It is an era of circular manufacturing, an era where sustainability takes center stage, waste becomes a valuable resource, and innovation empowers a greener future. In this article, we will explore the details of circular manufacturing, its benefits, and how it is shaping a more sustainable path for industries worldwide.
Circular manufacturing is a holistic approach to production that aims to eliminate waste and optimize resource utilization. It closes the loop by ensuring that materials are reused, recycled, or repurposed at the end of their lifecycle. Unlike the traditional linear model of “take-make-dispose,” circular manufacturing embraces a regenerative and restorative principle, where the concept of waste is challenged, and materials flow within a closed-loop system. Circular manufacturing enables manufacturers to:
This shift in manufacturing will help minimize environmental impact, realize cost savings, become less resource intensive, and be flexible enough to make design and material adjustments.
According to a report by Ellen Mac Arthur Foundation, circular manufacturing can result in massive material cost savings, amounting to USD 700 billion per year globally. Manufacturers are increasingly realizing the need to become circular to recognize these material savings and minimize their environmental impact.
Currently, businesses discard about 80% of the value of the materials in consumer goods and don’t recover them. The shift to an industrial circular economy has the potential to generate $2 trillion by the year 2030 alone, reports McKinsey.
Design for Circularity: Circular manufacturing begins at the design stage, where products are conceived to meet the demands of the circular economy. The designing process is done with longevity, recyclability, and ease of disassembly in mind. By incorporating modular components, renewable materials, and minimal waste generation, products are built to last and can be efficiently recovered at the end of life.
Resource Optimization: Circular manufacturing emphasizes the efficient use of resources like energy, water, and other raw materials. Companies strive to minimize waste through lean manufacturing practices, recycling, and reusing materials wherever possible.
Extended Producer Responsibility: Manufacturers take full responsibility for their products throughout their lifecycle, implementing take-back programs, recycling initiatives, and product stewardship policies to ensure proper disposal or repurposing.
Environmental Preservation: By reducing the consumption of resources, minimizing waste generation, and promoting recycling, circular manufacturing significantly reduces the environmental footprint of every industry. It conserves natural resources, protects ecosystems, and reduces pollution, contributing to a healthier planet for future generations.
Cost Savings: Circular manufacturing presents opportunities for companies to reduce their cost through improved resource efficiency, reduced waste disposal costs, and the creation of new revenue streams from recycled or repurposed materials.
Enhanced Resilience: By embracing circularity, businesses are better equipped to navigate supply chain disruptions, resource scarcity, and regulatory changes. They build resilience by diversifying supply sources, reducing dependence on virgin resources, and fostering innovation.
Closed-Loop Recycling: Companies like Patagonia and Nike have efficiently implemented closed-loop recycling programs, where products are collected, disassembled, and transformed into new materials for future production.
Product-as-a-Service (PaaS): Brands like Philips and Mud Jeans are developing the concept of leasing or renting products instead of selling them, allowing for better resource management, maintenance, and end-of-life recovery.
Industrial Symbiosis: Just like in biology, in industrial symbiosis, companies in the same locality collaborate to exchange waste materials, energy, or by-products, reducing waste generation and optimizing resource utilization.
Advancements in technology, such as additive manufacturing (3D printing), Internet of Things (IoT), and artificial intelligence (AI), are catalysts for circular manufacturing. These technologies enable precise material usage, efficient production, and enhanced product lifecycle tracking, facilitating the transition to a circular economy.
Circular manufacturing represents a powerful shift in the way we produce and consume goods, offering immense potential for environmental preservation, economic benefits, and improved resilience. By embracing the principles of circularity, businesses can contribute to a more sustainable future, where waste becomes a thing of the past, and resources are utilized in a regenerative and responsible manner. As we embark on this transformative journey, remember that through circular manufacturing, we have the power to create a world where sustainability and prosperity go hand in hand.
With the rising concerns in environmental sustainability, procurement practices are very crucial in driving …
In a world that faces growing environmental challenges especially in waste management, the concept of a …
In our quest for sustainable development, it is crucial to understand the environmental impacts of products …